Усиление сварного шва рассматривается как процесс добавления дополнительного металла или увеличения размеров существующего шва. При этом повышается несущая способность соединения, и снижается риск образования трещин при нагрузках. Эта технология необходима при изготовлении и обслуживании конструкций, работающих под высокими нагрузками, в том числе вибрационными или динамическими. Своевременное усиление помогает продлить срок службы изделий и улучшить их эксплуатационные характеристики.
В материале рассмотрены особенности усиления стыковых и угловых швов, а также способы контроля качества сформированных соединений. Дополнительно представлен чек-лист, по которому можно отличить реальное производство от посредников.
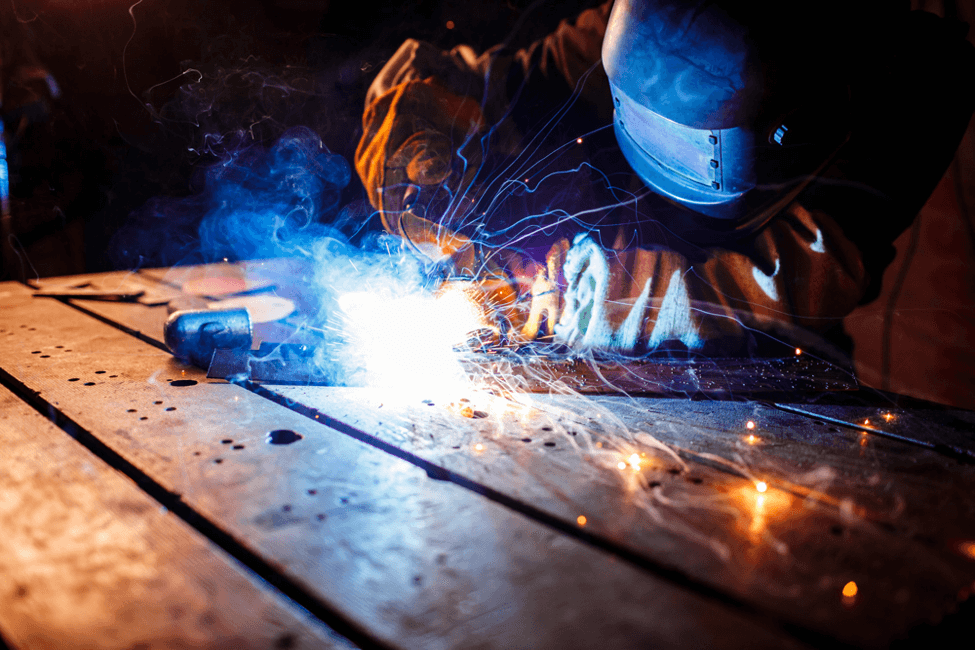
Специфика усиления сварных швов
Усиление шва чаще всего включает увеличение длины валика либо его ширины и высоты. В стыковых соединениях при такой процедуре стараются исключить концентрацию напряжений в одном месте, поэтому предпочтение отдают распределению металла по большей площади.
Когда детали соединяются встык, внутренняя структура металла может испытывать высокие механические напряжения. Если оставить зону сварки с минимальным припуском, возрастает вероятность развития скрытых дефектов, приводящих к скорому разрушению конструкции.
Оптимальный объем наплавки определяется с учетом назначения изделия, толщины деталей и условий эксплуатации. В некоторых случаях усиливают только участки, где прогнозируются максимальные нагрузки, чтобы сэкономить материалы и не подвергать конструкцию лишнему термическому воздействию.
Чтобы понять, насколько увеличивать размеры наплава, ориентируются на требования соответствующих ГОСТ и строительных норм. Чрезмерное усиление вызывает перегрев металла и образование хрупких зон, поэтому необходимо тщательно соблюдать регламентированные значения катетов.
К основным факторам, влияющим на выбор стратегии усиления, относят:
- Толщину основного металла.
- Тип сварного соединения (стык, угол, тавр).
- Наличие внутренних дефектов.
- Уровень ожидаемых рабочих нагрузок.
Основные стандарты, используемые при усилении
Единые требования к усилению сварных швов закреплены в целом ряде нормативных документов. Большое значение имеет ГОСТ 2.301 и его дополнения, регулирующие размеры катетов, допуск на высоту наплава и другие параметры.
Также существуют стандарты, определяющие технологию послойной наплавки. Каждый слой рекомендуется формировать электродами диаметром 3–4 мм, а переходить к следующему можно только после остывания предыдущего до приблизительно +100 °С.
При работе с угловыми швами допускается использование катетов, не превышающих толщину полки уголка со стороны пера и полутора толщин со стороны обушка. Нарушение этого правила повышает риск возникновения напряженных зон и трещин при дальнейшей эксплуатации.
Для снижения концентрации остаточного напряжения рекомендуется плавно распределять наплавленный металл, избегая внезапных перепадов по высоте. Если речь идет о конструкциях, где важна герметичность, усиливать швы лучше постепенно, с обязательным контролем качества каждого прохода.
При выборе стандарта ориентируются:
- На толщину деталей и их конфигурацию.
- Климатические и эксплуатационные условия.
- Типы нагрузок (статические, вибрационные).
- Специальные требования отрасли (судостроение, нефтегаз).
Усиление стыковых швов
Стыковые швы чаще всего выполняются по всей длине стыкуемых деталей, что исключает возможность многократного увеличения ширины наплава без риска перегрева. Иногда усиление таких швов ограничивают только участками, где обнаружены трещины или недостаточный проплав.
Если в чертеже нет прямого указания на высоту усиления, ориентируются на стандартные значения, соответствующие толщине стыкуемых элементов. Чрезмерная выпуклость может препятствовать правильному распределению внутренних сил и привести к растрескиванию.
В случае критических дефектов применяют так называемый метод «заварки» с предварительным удалением поврежденного участка. Сначала шлифовкой снимают верхний слой наплава, затем вносят дополнительные слои металла, строго контролируя режимы нагрева и охлаждения.
Вычисляя нужные параметры усиления, используют формулы, учитывающие несущую способность наплава, расчетную площадь сечения и сопротивление материала. Для упрощения обычно берут готовые таблицы из нормативных документов, где уже прописаны необходимые корректировки.
Основные шаги при усилении стыкового шва:
- Диагностика с помощью дефектоскопии.
- Удаление бракованного участка.
- Послойная наплавка с контролем каждого прохода.
- Финальная проверка качества сварного соединения.
Усиление угловых стыковочных швов
Угловые соединения имеют свойство концентрировать напряжение в зоне катетов, поэтому при их усилении предпочитают увеличивать длину. Расширение площади контакта позволяет равномерно распределить нагрузки, не перегружая отдельные зоны металла.
Высота катета при формировании углового соединения влияет на надежность крепления обеих сторон детали. Если один катет получается короче второго, то нагрузка распределяется неравномерно, что повышает вероятность трещинообразования.
При усилении углового шва необходимо учитывать, что наплавка дополнительных слоев с каждой стороны может сместить центр тяжести конструкции. Если проектом это не предусмотрено, узел может испытывать избыточный изгибной момент во время эксплуатации.
В случае увеличения высоты катета более чем на 20% от исходной толщины детали желательно контролировать термический режим особо тщательно. Применяют интервалы охлаждения между каждым проходом и избегают избыточной скорости сварки, чтобы не допустить перегрева шва.
Допустимо укрепить угловое соединение путем введения накладок, которые увеличивают длину зоны сварки. Такой метод позволяет снизить вероятность дефектов в самом теле шва, поскольку нагрузка перераспределяется по дополнительным пластинам.
Снятие усиления сварного шва
На некоторых чертежах встречается примечание о необходимости удаления излишнего наплавленного металла после сварки. Это нужно, чтобы избежать опасных утолщений, где скапливаются напряжения, и может возникнуть усталостная трещина при циклических нагрузках.
При стыковых швах снятие усиления часто делают до уровня заподлицо с основной поверхностью. Таким образом повышают аэродинамические или гидродинамические свойства изделия, если оно используется в среде с повышенным давлением или потоком.
Угловые соединения требуют оставлять рассчитанный катет, соответствующий требованиям по прочности и нормативным документам. Если высота катета превышает рекомендованные значения, ее корректируют, сохраняя равномерность переходов на кромках.
Чаще всего снятие усиления выполняется механически – абразивными кругами, шлифовкой или прокаткой роликами. Если выявляются скрытые дефекты, удаляют все сомнительные участки, а затем заново наплавляют металл под контролем специалиста.
Основные причины, по которым снимают излишний наплав:
- Уменьшение концентрации напряжений.
- Улучшение внешнего вида конструкции.
- Сокращение риска появления вибрационных трещин.
- Обеспечение соответствия параметрам чертежа.
Методы контроля качества сварных соединений
Прежде чем приступать к усилению, проводят первичный контроль, чтобы исключить дальнейшее развитие дефектов. На этом этапе определяют вид сварки, подбирают расходные материалы, устанавливают подходящий температурный режим и проверяют настройку оборудования.
Окончательная проверка качества соединений бывает разной. В отдельных случаях хватает визуального осмотра с оценкой формования шва, но чаще используют неразрушающие методы, позволяющие глубже заглянуть внутрь металла.
Радиографический контроль предусматривает съемку сварного участка рентгеном или гамма-излучением. На пленке или цифровом снимке можно увидеть поры, расслоения, пустоты, определить геометрию шва и оценить реальную картину проплавления.
Ультразвуковая дефектоскопия более мобильна и востребована во многих отраслях. Специалист направляет волну в толщу металла и видит отражения от внутренних границ, что помогает выявить трещины и другие опасные зоны без разрушающего вмешательства.
Магнитопорошковый метод актуален для ферромагнитных сталей. Намагниченные частицы оседают вокруг дефектов, визуально указывая место расположения трещин. Гидравлические и пневматические испытания проводят в трубопроводах и емкостях, чтобы проверить герметичность швов.
Иногда применяют вакуумный контроль. На поверхность шва наносят тонкий слой мыльного раствора и прикладывают вакуумную камеру. При наличии мельчайшей неплотности образуются пузырьки, позволяющие точно определить место утечки.
Популярные методы неразрушающего контроля:
- Радиографический (рентген, гамма).
- Ультразвуковой (эхо-сигнал).
- Магнитопорошковый (намагничивание).
- Гидравлические и пневматические испытания.
- Вакуумная проверка целостности.
Подробный чек-лист для отличия реального производства от посредников
При заказе услуг металлообработки важно убедиться, что исполнитель действительно обладает собственным оборудованием и квалифицированными сварщиками. Перекупщики часто передают работу на субподряд, не контролируют технологию и не несут ответственности за дефекты.
Обращайте внимание на наличие документации и прозрачность расчетов. Если предприятие готово показать сертификаты, лицензии, чертежи, примеры реальных проектов и оформить все договора официально, это свидетельствует о том, что у него есть производственная база.
У добросовестного исполнителя обычно представлены фотографии оборудования, цехов, готовой продукции. Он может предоставить гарантии на сварные швы, поскольку контролирует качество на каждом этапе и не перекладывает риски на третьих лиц.
Изучение отзывов помогает понять, как компания решает спорные моменты, соблюдает ли сроки и обеспечивает ли стабильное качество. Попросите связаться с реальными клиентами, которые могут подтвердить, что работы выполнены точно по заданным параметрам.
Если вам предлагают скачать чек-лист для выбора подрядчика, изучите пункты по оборудованию, квалификации персонала, режимам сварки, доступным методам контроля и наличию необходимых разрешений. Чем детальнее подобный список, тем выше вероятность, что перед вами реальное производство, способное решать нестандартные задачи.
23.01.2025Читайте также другие статьи по теме:
ВсеВам могут быть интересны наши услуги:
Отдавая нам в работу ваш проект, вы получаете четко выполненные изделия по низким ценам в обозначенные сроки.
Мы можем помочь в проектировании заказа или доработаем ваш макет.
Прикрепите фото, эскиз или чертеж и получите бесплатный расчет в течении 20-30 минут.
Получите расчет в течении
20-30 минут
Сделайте эскиз или набросок на бумаге и укажите необходимые размеры, а мы переведем все в чертеж и произведем расчет.